 |
|  |
|
Quality Manager
Job Summary
Support and coordinate all aspects all of the facility quality assurance and control program for the organization. Investigate and resolve customer complaints regarding quality. This may entail technical responses to written claims and complaints. Complete on site visits to customer facilities, negotiate with customer quality representatives and/or report process capabilities and out of scope issues to interested customers and management personnel.
Essential Duties And Responsibilities
- Coordinate the objectives with production management and manufacturing procedures in order to maximize product reliability and minimize costs associated with rework, scrap.
- Detect and provide scrap data to management in such a way that analysis and corrective actions can take place.
- Monitor progress and work in cooperation with other Supervisors / Managers
to develop methods and procedures that affect continual quality improvement.
- Maintain within levels of stress, deadlines, and occasional extended schedules.
- Understand cert’s associated with Zinc, Cad, Tin, and Anodize.
- Develop a cooperative, professional relationship with manufacturing in order to facililitate and coordinate functions and operations between department’s procedures and criteria for attaining quality and manufacturing products.
- Manage the quality systems associated with IS9001 and AS9100, PPAP, and FOD.
- Understand and manage the quality systems associated with heat treat.
- Provide simple and complex written and spoken communication links.
- Review and monitor processes within the department on a continuous basis for effectiveness and possible improvements.
- Knowledge of ROHS Compliance and prohibited material restrictions required.
- Must be able to read, understand and interpret engineering drawings and complex blueprints.
- Relate drawings and prints to raw material selection, outside processes, and manufacturing processes.
- Identify and resolve potential problems between prints / travelers / manufacturing processes.
- Administer routings, bills of material, QPA from a traveler.
- Basic understanding of work centers and their processes.
- Including production equipment.
- Including compound insert and tooling departments.
- Excellent communication and organizational skills.
- Customer Service Support, answering technical questions on engineering level.
- Work with, specify, and troubleshoot existing manufacturing systems and make recommendations for process improvements.
- Show attention to detail.
- Demonstrate ability to make sound judgments.
- Good computer skills.
- Must be able to work within deadlines.
- Interact with all company departments.
- Work in a safe and professional manner, keeping a clean work area and wearing proper protective equipment.
- Cooperation with supervisor and co-workers, willing to work as a team.
- Show by example: temperament, professionalism and teamwork.
- Timely arrival and regular attendance at work.
- Willing to work overtime.
- Willing to work any shift.
- Other duties may be assigned.
Supervisory Responsibilities
- All quality inspectors will report to the Quality Manager
Qualifications
- To perform this job successfully, an individual must be able to perform each of the essential duties satisfactorily. The requirements listed above are representative of the knowledge, skill and/or ability required. Reasonable accommodations may be made for individuals with disabilities for perform the essential functions.
Technical Skills
Education and/or Experience
- Bachelor degree or an equivalent combination of education and experience. Must be computer and, using both PC and mainframe systems for information retrieval and analysis. Must have a background in manufacturing processes.
Language Skills
- The ability to read, write and speak the English language with comprehension skills sufficient to understand safety standards and job performance expectations.
Mathematical Skills
- The ability to add, subtract, multiply, and divide in all units of measure, using whole numbers, common fractions, and decimals, as well as the ability to compute rate, ratio, and percent and to draw and interpret bar graphs.
Reasoning Ability
- Ability to define problems,collect data, establish facts, and draw valid conclusions. Ability to interpret an extensive variety of technical instructions in mathematical or diagram form as well as deal with several abstract and concrete variables.
Certificates, Licenses, Registrations
Work Environment
- While performing the duties of this job the employee is subject to inside environmental conditions and regularly exposed to loud noise. The employee may also have air and/or skin exposure to oils and other cutting fluids. The employee will on occasion be exposed to moving mechanical parts in a high noise level environment.
- The noise level in the environment is quiet to loud.
Physical Demands
- While performing the duties of this job, the employee is regularly required to sit and stand; use hands to finger, handle, or grab; reach with hands and arms; and talk and hear. The employee frequently is required to walk. The employee at times will stoop, kneel, crouch and reach. The employee is frequently required to lift and/or move 10 pounds and occasionally lift and/or move up to 50 pounds. Specific vision abilities required by this job include close vision, distance vision, depth perception and the ability to adjust focus.
- While performing the duties of this job, the employee is regularly required to talk and hear. The employee frequently is required to walk, stand and sit. The employee is required to use hands to finger, handle or feel and reach with hands and arms. Repetitive motions, such as those used for computer keyboard data entry are also required.
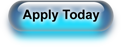
|
|
 |
|  |
|